
BLOG
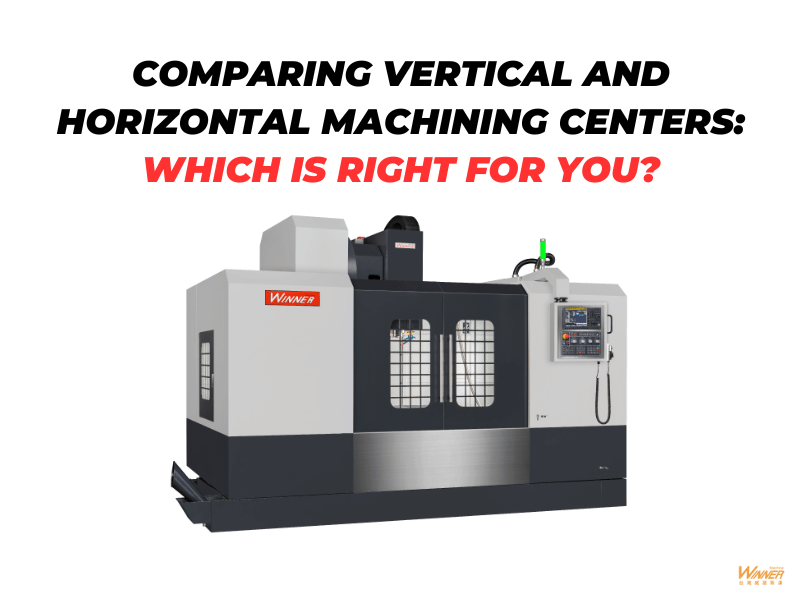
When setting up or expanding a manufacturing facility, one of the key decisions you'll face is choosing between a vertical machining center (VMC) and a horizontal machining center (HMC). Each type has distinct advantages and is suited to different applications and preferences. Understanding these can help you make an informed decision that optimizes productivity, cost-efficiency, and quality in your operations.
Vertical Machining Centers (VMCs)
Design and Operation: VMCs feature a vertically oriented spindle where tools spin while the workpiece is mounted on a stationary bed below. This configuration is especially beneficial for plate, die, and sheet material work.
Advantages:
- • Accessibility: VMCs offer easy access to the spindle and workpiece, making setup and tool changes simpler and quicker.
- • Cost-Effectiveness: Generally, VMCs are less expensive than HMCs, both in initial cost and maintenance. They consume less floor space, which can reduce facility costs.
- • Versatility: Ideal for applications that require a high degree of detail and precision, such as milling, drilling, and tapping.
Best Uses:
VMCs are preferred for jobs that require quick tool access and fine, detailed work, making them popular in automotive, aerospace, and electronics manufacturing.
Horizontal Machining Centers (HMCs)
Design and Operation: In contrast to VMCs, HMCs have a spindle that is oriented horizontally. Workpieces are attached to a pallet that moves in the X, Y, and Z axes, while the cutting tool moves across them.
Advantages:
- • Increased Cutting Power: The horizontal orientation allows for more aggressive and faster cutting without compromising tool life.
- • Better Chip Evacuation: Gravity assists in removing chips from the workpiece, reducing the risk of surface defects on finished products.
- • Pallet Changing System: Many HMCs come with a rotating pallet feature, which allows one part to be loaded/unloaded while another is being machined, significantly reducing downtime.
Best Uses:
HMCs are typically used for heavier and larger workpieces or for high-volume production runs. They excel in environments requiring extensive milling, such as the production of engine components in the automotive industry or heavy equipment manufacturing.
Which is Right for You?
Consider Production Volume:
- • If your operation requires high-volume production with less downtime between operations, an HMC might be the better option due to its pallet changer system.
- • For lower-volume, high-precision tasks, a VMC is typically sufficient and more cost-effective.
Assess Part Complexity:
- • HMCs are generally preferred for complex parts that require multi-face machining in a single setup.
- • VMCs are suitable for simpler parts or when only a few sides of a part need to be machined.
Evaluate Facility Space and Budget Constraints:
- • If space is a premium or budget is limited, a VMC could be a more suitable choice. It requires less floor space and is less costly both in terms of initial investment and operational overhead.
- • HMCs, though more expensive, provide greater throughput and may justify the additional expense through higher productivity.
Conclusion
Choosing between a vertical and horizontal machining center depends largely on the specific needs of your production processes, including the volume, part complexity, and space constraints of your operations. By carefully assessing these factors, you can select a machining center that not only fits your current needs but also scales with your future growth. In either case, both VMCs and HMCs offer distinct advantages that can enhance the efficiency and quality of your manufacturing output.
If you are interested in purchasing a VMC and need guidance to select the right machine for your business needs, please contact us at Taiwan Winnerstech. Our team of experts is ready to help you with detailed product information and tailored advice, ensuring you make the best choice for your manufacturing operations.