
BLOG
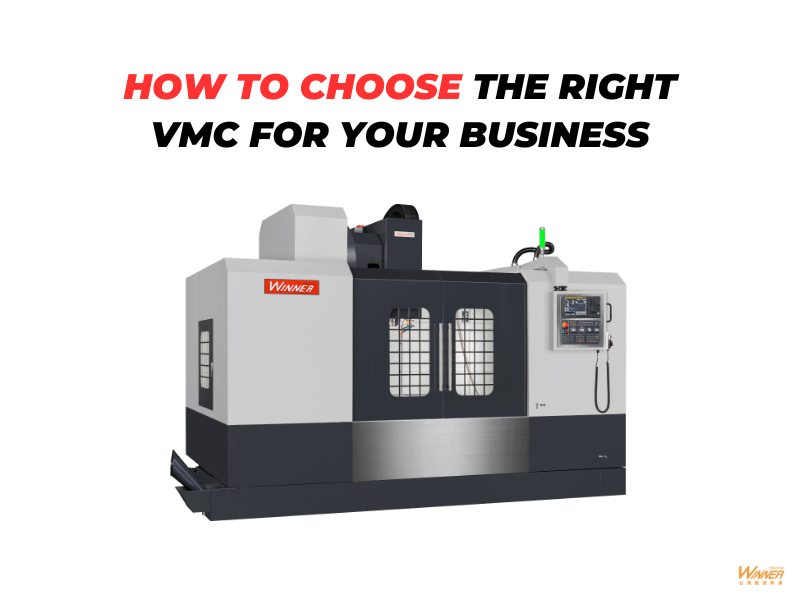
Selecting the right Vertical Machining Center (VMC) is crucial for manufacturing businesses that aim to enhance productivity, maintain precision, and optimize operational efficiency. VMCs are versatile and powerful tools, but with many models and features available, choosing the one that best fits your specific needs can be challenging. This article outlines key considerations to help you select the ideal VMC for your operations.
1. Understand Your Machining Requirements
The first step in selecting a VMC is a thorough assessment of your manufacturing needs:
- Part Dimensions and Tolerances: Consider the size and precision requirements of the parts you will produce.
- Material Types: Different materials require different spindle types and cutting tools.
- Production Volume: High-volume manufacturing may need a more durable machine with rapid cycle times and minimal downtime.
2. Evaluate Machine Specifications
- Work Envelope and Table Size: Ensure the VMC can accommodate the largest parts you plan to machine. Check both the X, Y, and Z-axis travel and the table load capacity.
- Spindle Performance: Spindle speed (RPM), power (horsepower), and torque determine the machine’s ability to cut various materials. Higher speeds are better for softer materials and fine, detailed work, while higher torque is necessary for harder materials.
- Tool Storage Capacity: A larger automatic tool changer (ATC) reduces setup time and increases run times, essential for complex parts with multiple tooling requirements.
3. Consider Advanced Features
- Multi-axis Capability: Machines equipped with fourth or fifth-axis capabilities allow for more complex geometries without additional setups.
- High-speed Options: Advanced high-speed machining options can significantly reduce milling time and improve surface finish.
- Automation Integration: Consider VMCs that can easily integrate with robotic systems if you're planning towards full automation.
4. Control System Compatibility
- User Interface: Choose a control system that is user-friendly and compatible with your operators’ skills and your CAD/CAM software.
- Software Features: Look for features that simplify programming and can enhance machine productivity, such as predictive maintenance tools, remote monitoring, and diagnostics capabilities.
5. Assess Accuracy and Precision
- Manufacturing Tolerances: Ensure the VMC can consistently meet the tolerances required by your applications.
- Thermal Stability: Some machines offer enhanced features to minimize thermal growth and improve accuracy over long operation periods.
6. Calculate Total Cost of Ownership
- Initial Investment vs. Long-term Benefits: Weigh the upfront cost against the expected productivity gains, energy efficiency, and maintenance costs.
- Maintenance and Support: Ensure the manufacturer provides comprehensive training, timely maintenance, support services, and spare parts availability.
7. Look for Reliable Manufacturers
- Reputation and Reviews: Research manufacturers for their reliability and service quality. Reviews and testimonials can provide insight into the longevity and performance of their machines.
8. Plan for Future Needs
- Scalability: Consider whether the VMC can adapt to future growth. This might include options for additional axes, larger tool magazines, or software upgrades.
Conclusion
Choosing the right VMC requires a balance of current needs and future growth potential. By carefully considering the factors outlined above, you can select a VMC that not only meets your manufacturing requirements but also offers flexibility to adapt as your business evolves. This strategic approach ensures that your investment in a VMC propels your manufacturing capabilities forward, supporting sustained business growth and competitiveness in your industry. At Taiwan Winnerstech, we are dedicated to helping you find the perfect machining solutions that align with your specific production goals and enhance your operational efficiency.