
BLOG
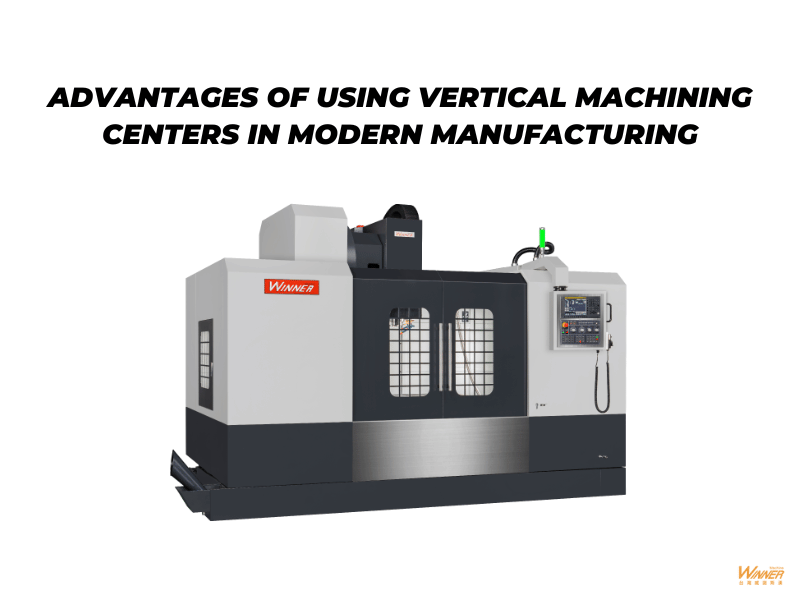
In our previous exploration of what a Vertical Machining Center (VMC) is, we introduced the basic structure and operational principles of VMCs. Building upon that foundation, this article delves into the specific advantages that make VMCs indispensable in modern manufacturing settings. Understanding these benefits not only highlights the versatility of VMCs but also demonstrates why they are increasingly favored in industries demanding precision and efficiency.
Enhanced Precision and Quality
- High Accuracy: VMCs are designed to achieve tight tolerances with excellent repeatability, making them ideal for precision-critical industries such as aerospace and medical device manufacturing.
- Consistent Quality: Automated operations reduce human error and ensure consistent quality across large production volumes, crucial for maintaining standards in consumer electronics and automotive manufacturing.
Increased Efficiency and Productivity
- Reduced Setup Time: Advanced tooling systems with automatic tool changers drastically cut down setup time, enabling quicker job transitions.
- Continuous Operation: Many VMCs can operate unattended, using sophisticated software to manage tasks overnight or during off-hours, significantly boosting productivity.
Versatility in Applications
- Multi-functionality: Capable of performing various operations like milling, drilling, and tapping, which eliminates the need for multiple machines.
- Material Flexibility: Effective on a wide range of materials including alloys, plastics, and composites, enabling manufacturers to use one machine for different manufacturing needs.
Reduced Operational Costs
- Lower Initial Investment: Compared to purchasing multiple specialized machines, investing in a VMC reduces upfront costs.
- Decreased Maintenance Costs: VMCs often require less maintenance than older or more specialized equipment, owing to their advanced design and fewer mechanical components.
Improved Safety
- Enclosed Operation: The cutting area is fully enclosed, reducing the risk of operator injury from flying debris or moving parts.
- Automated Controls: Operators control VMCs from a computer console, which minimizes the need for direct contact with the machine's moving parts.
Scalability and Flexibility
- Easy Upgrades: Many VMC models are designed to allow easy upgrades like additional spindles or rotary tables, accommodating business growth without extensive re-investment.
- Adaptive Software Integration: VMCs can be updated with new software to handle evolving production technologies and processes.
Integration with Modern Manufacturing Systems
- CAD/CAM Compatibility: Direct integration with CAD/CAM systems allows for smooth transitions from design to production, enhancing the speed and accuracy of manufacturing.
- IoT Connectivity: Many newer VMCs are equipped with IoT capabilities, enabling predictive maintenance, real-time monitoring, and enhanced data analytics.
Conclusion
VMCs significantly enhance manufacturing capabilities through their precision, efficiency, and integration with modern technological advances. As industries continue to evolve, VMCs remain crucial in meeting the growing demands for higher quality and faster production rates. Whether tackling complex components for aerospace or straightforward parts for consumer electronics, VMCs provide the reliability and performance necessary to succeed in today's competitive marketplace. At Taiwan Winnerstech, we are committed to providing state-of-the-art machining solutions that help our customers achieve these goals effectively.